Veritx to use Algorand blockchain for aircraft supply chain
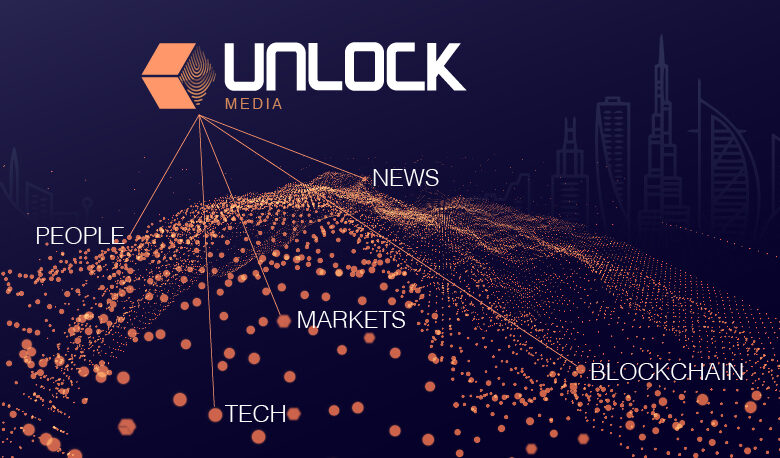
Veritx Corporation, marketplace for digital assets enabling decentralized manufacturing, will develop a digital supply chain for aircraft parts using the Algorand blockchain technology. The VeriTX digital marketplace allows customers such as the Department of Defense and commercial airlines to save significant time and money in manufacturing aircraft parts and to gain valuable economic and logistical data that can be used to maximize efficiency. As the US Army, Navy and Air Force all move toward a digital supply chain, the combined market size for digital aircraft parts is expected to reach $3.1B by 2025. An Air Force maintenance commander estimated VeriTX would yield a 30% cost savings, 90% reduction in waste, and a 25% increase in aircraft performance (uptime).
The VeriTX Platform, a digital marketplace that directly connects buyers and sellers of aircraft parts that can be 3D printed on-demand at the point of use, is building on Algorand’s public, pure proof-of-stake blockchain. This enables the additional benefits of tracking the parts from order to delivery on an immutable distributed ledger, and verifying the provenance (origin and authenticity) of the parts, mitigating the $3-billion problem of counterfeit parts.
“We chose Algorand as the blockchain infrastructure to power our platform, after looking at several technology providers and rigorous due diligence,” said Col James Allen Regenor, USAF (ret), VeriTX CEO. “Algorand was the ideal solution to onboard our ecosystem partners to the network, because of its flexible architecture, low transaction fees and transactional throughput scalability.”
Until now, the aerospace manufacturing industry has largely relied on business systems developed in the 1980s— ordering parts from printed catalogs via fax and phone. VeriTX will digitize and decentralize the parts manufacturing process by breaking it down into four steps:
- Sellers design parts digitally. This includes the idea, prototype and final design of parts ranging from traditionally forged metal engine parts to polymer-molded interior parts used in aircraft cabins.
- Sellers upload parts on VeriTX platform. All the necessary information such as pricing, specifications, and provenance is included.
- Buyers purchase digital parts. The platform enables the exchange of digital assets, which will eventually become tangible in the last step.
- Push to point-of-use, then 3D print. For those who do not have 3D printing machines, VertiTX has machine partners who can print the parts and have them ready for pick-up or delivery.
The impact of the VeriTX digital supply chain was proven with real-world use cases:
- F15-Eagle fighter metal aircraft parts: Typically takes 265 days from order to delivery. VeriTX reduced lead time exponentially to just 6 hours.
- Polymer aircraft parts: Time from order to delivery was reduced from 133 days to 1 hour. Since the process was entirely digital, once the part was ordered, it was sent instantly to the 3D printer, which was waiting. Making (printing) the part took about 40 minutes. It was made at the airline’s maintenance facility, so delivery was as soon as it was done.
- Commercial airline: During a flight from Auckland to Los Angeles, a cabin part failed that would put a business premier class seat out of operation. Using VeriTX, the airline was able to order a digital replacement and have this part manufactured in one hour. When the plane landed in LA, the part was installed and the cabin was back in operation. Lead time reduction 50x. Saved $30,000 in potential lost revenue from the cost of the seat and the cost of flights to get the needed part and make the repair.
“What VeriTX is doing—removing friction from transactions—is Algorand’s primary mission. VeriTX is applying the technology in a very tangible way that showcases the power of blockchain to reinvent established industries like manufacturing in a decentralized manner,” said W. Sean Ford, COO of Algorand. “Taking out the middleman, VeriTX is connecting buyers and sellers directly to maximize efficiency and actively reshape the future of manufacturing.”